Customer Satisfaction Is a Top Priority at PDC Machines
We have established a worldwide network of service providers to deliver local, prompt response to our customers’ inquiries. You can locate a Qualified PDC Service Provider through our website.
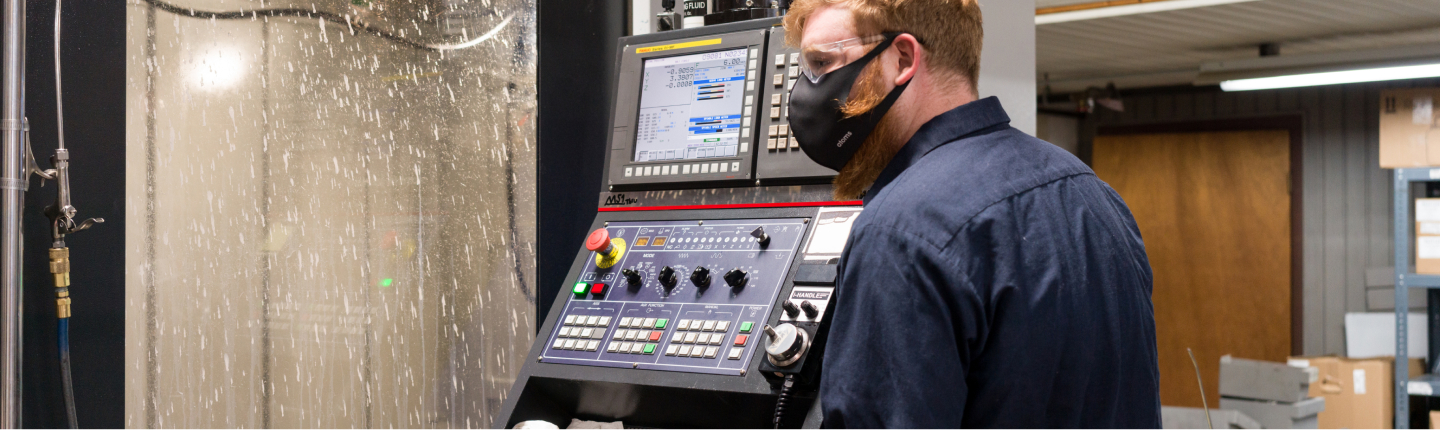
Maintenance
Maintenance Kits
Maintenance Kits Help Ensure Peak Performance
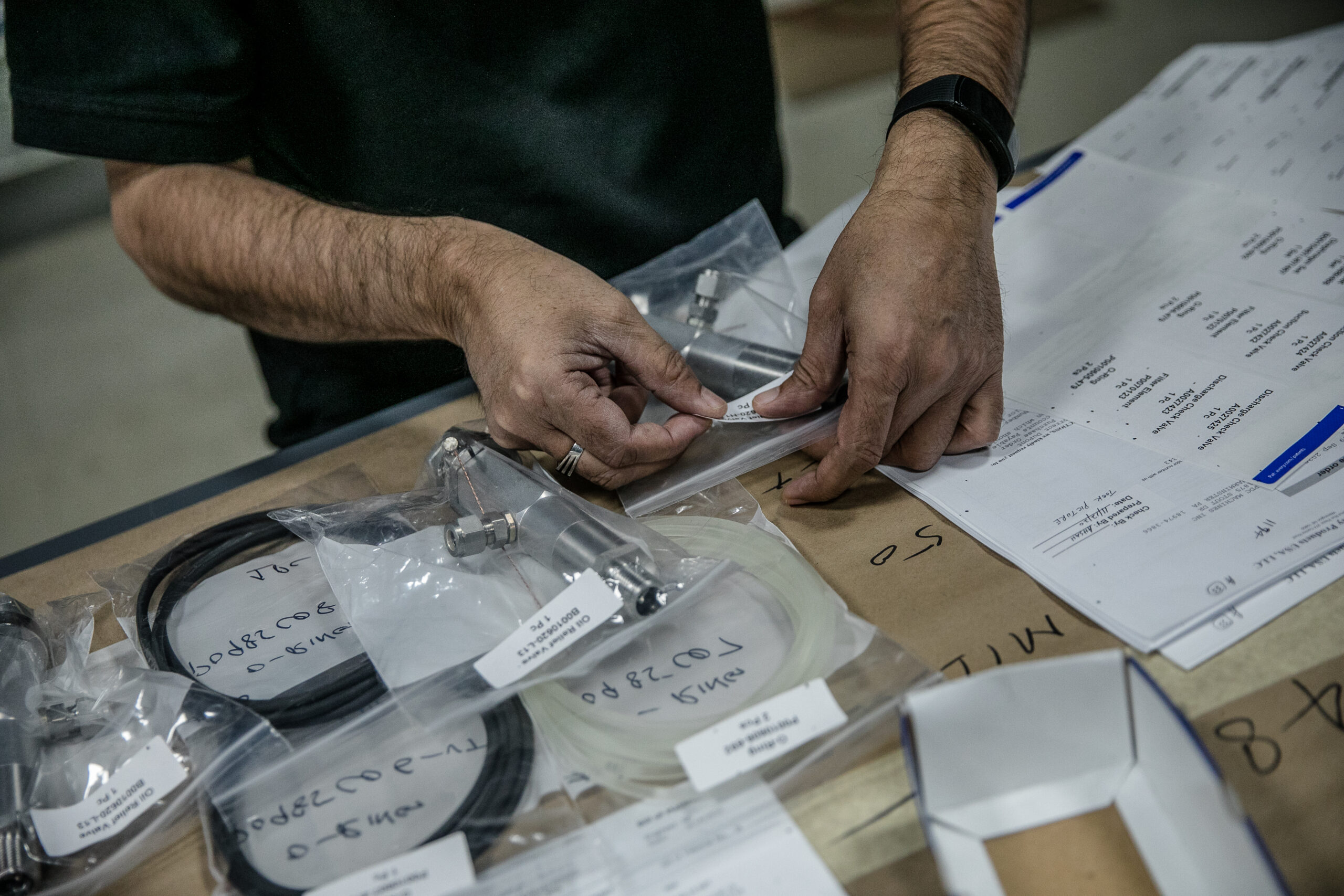
Spare Parts
Spare Parts
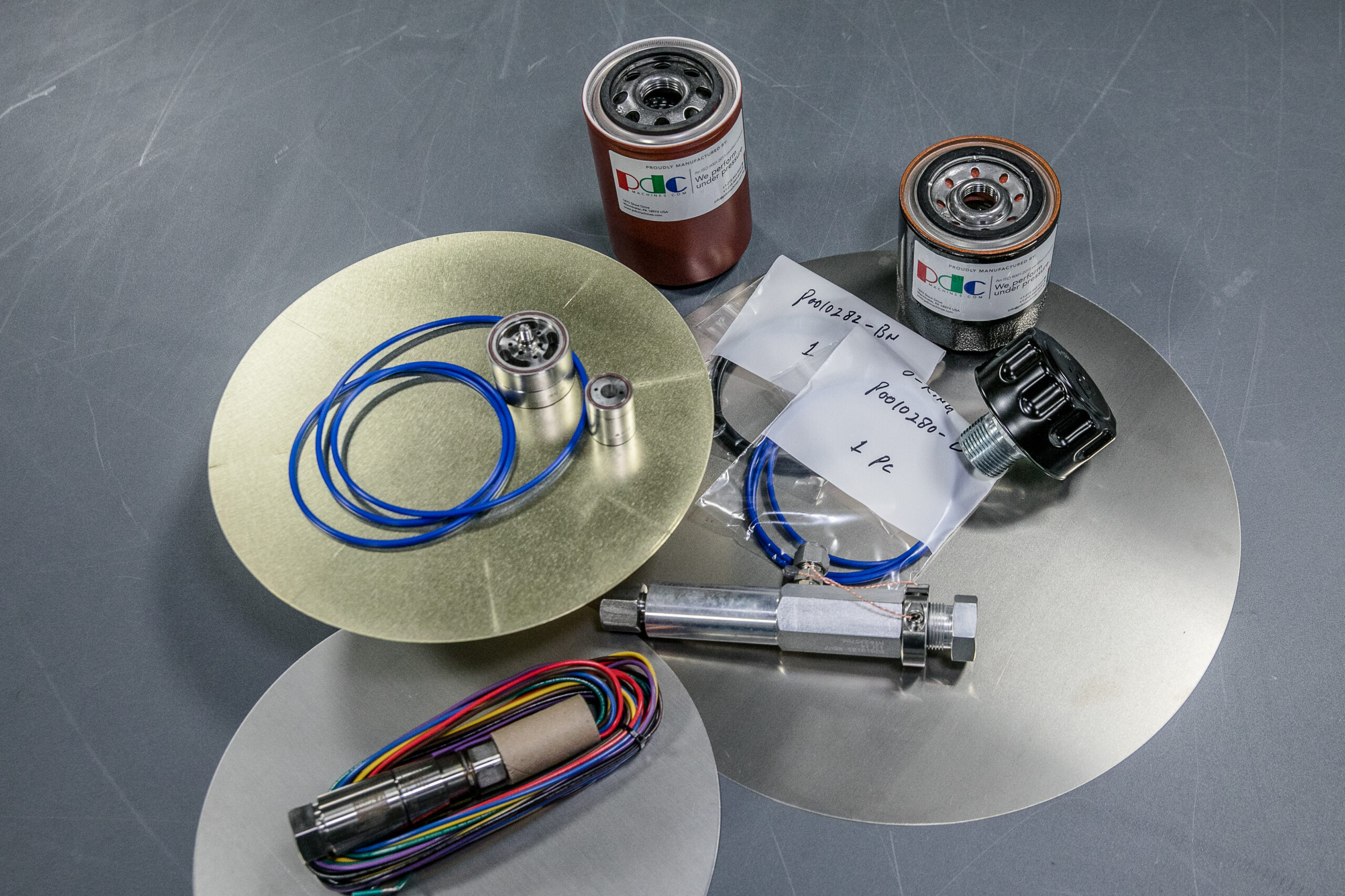
Ordering Spare Parts
Ordering Spare Parts
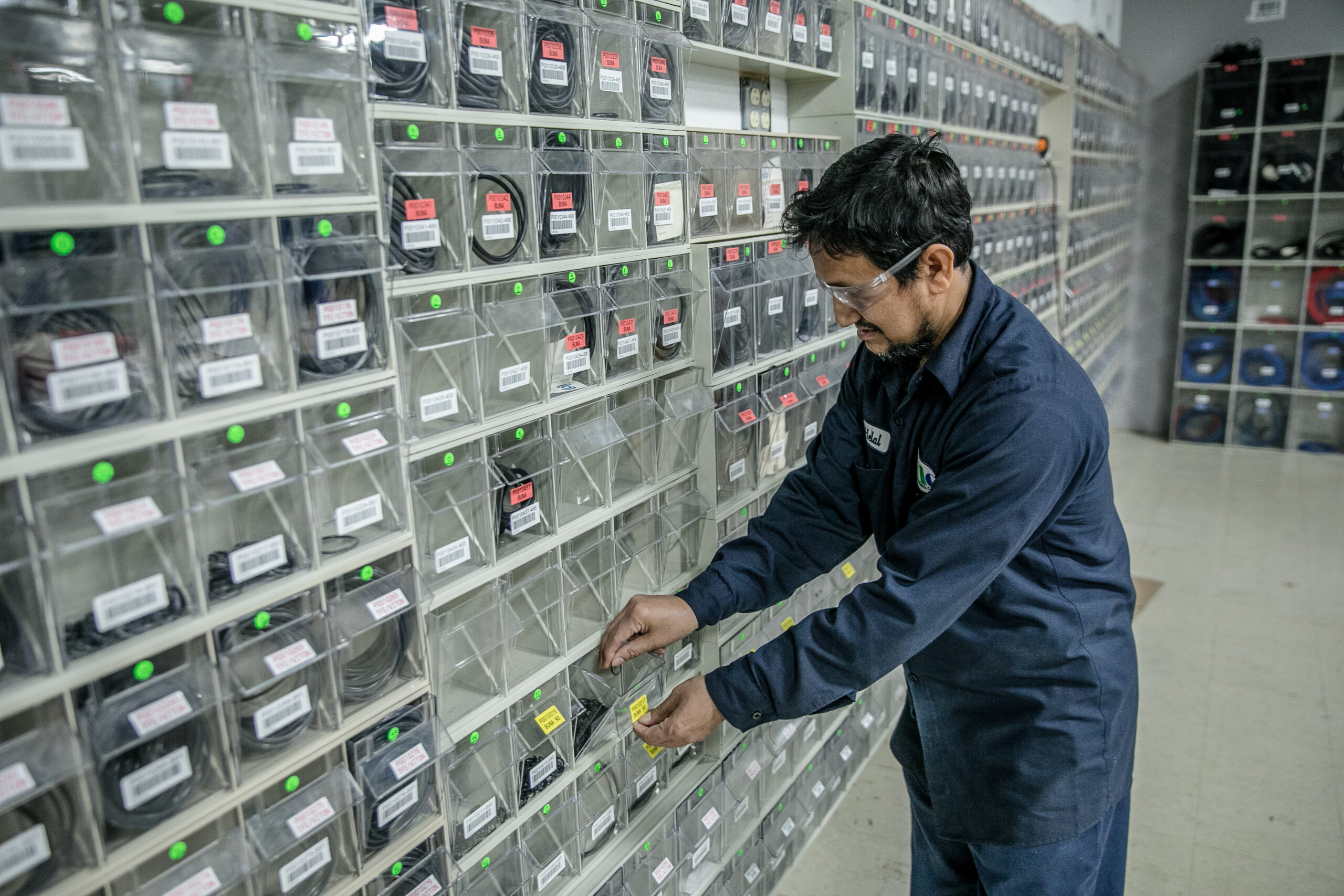
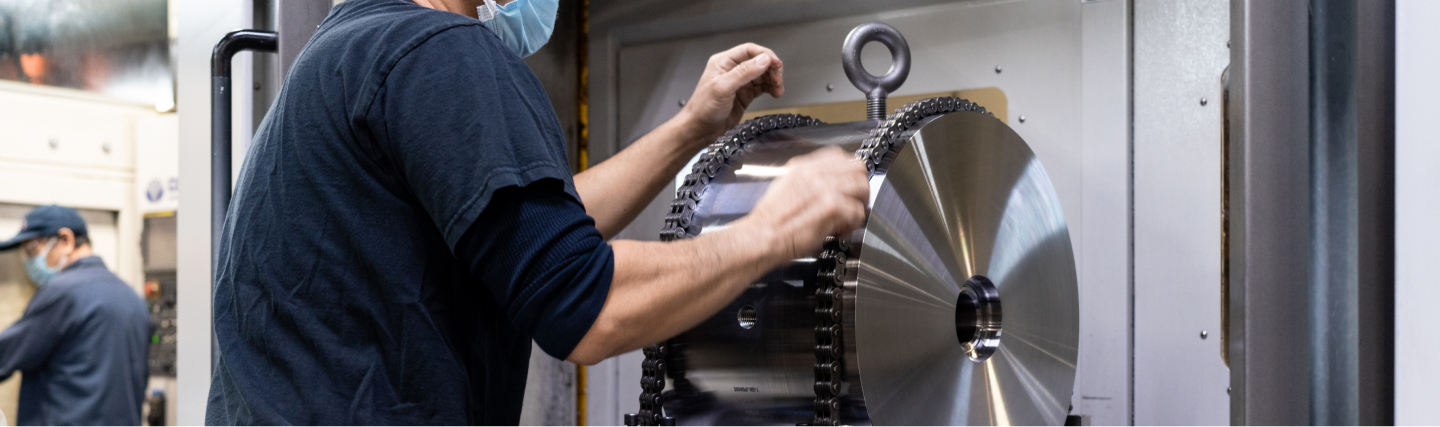
Service
Service Programs
Service Programs
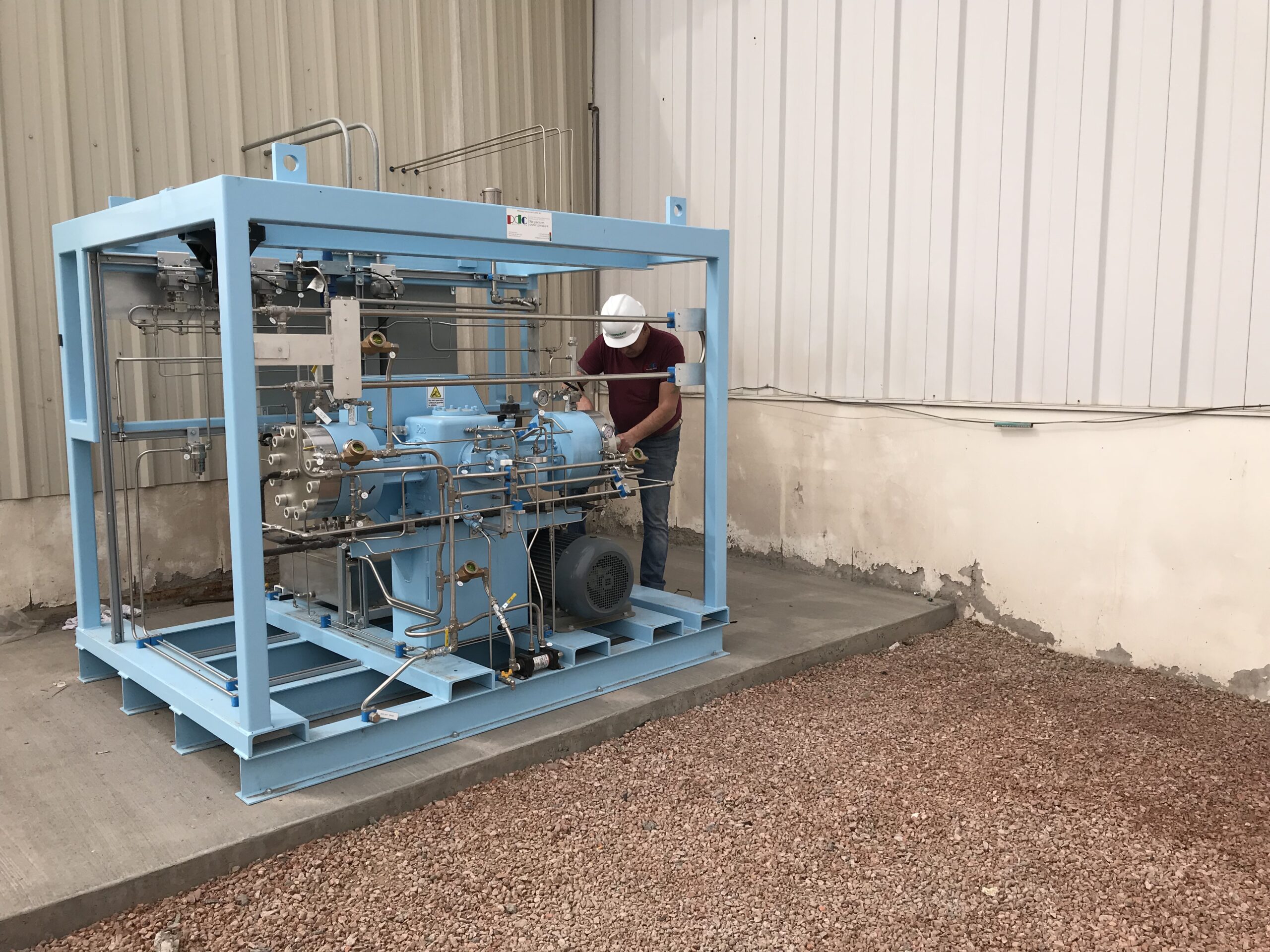
Operational Instructions
Operational Instructions
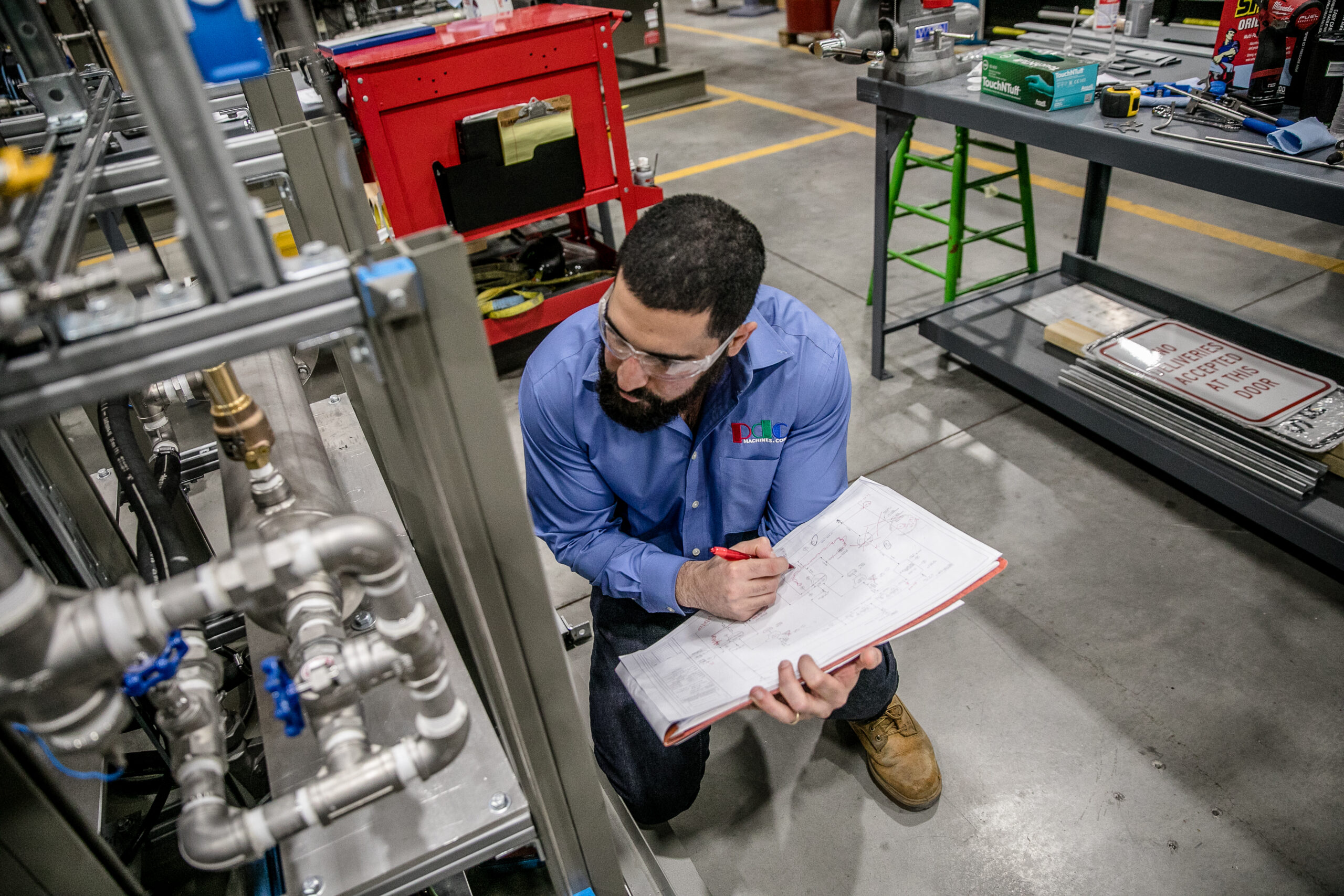
Operation and Preventative Maintenance Training
We can customize any training program that is right for you and your needs.
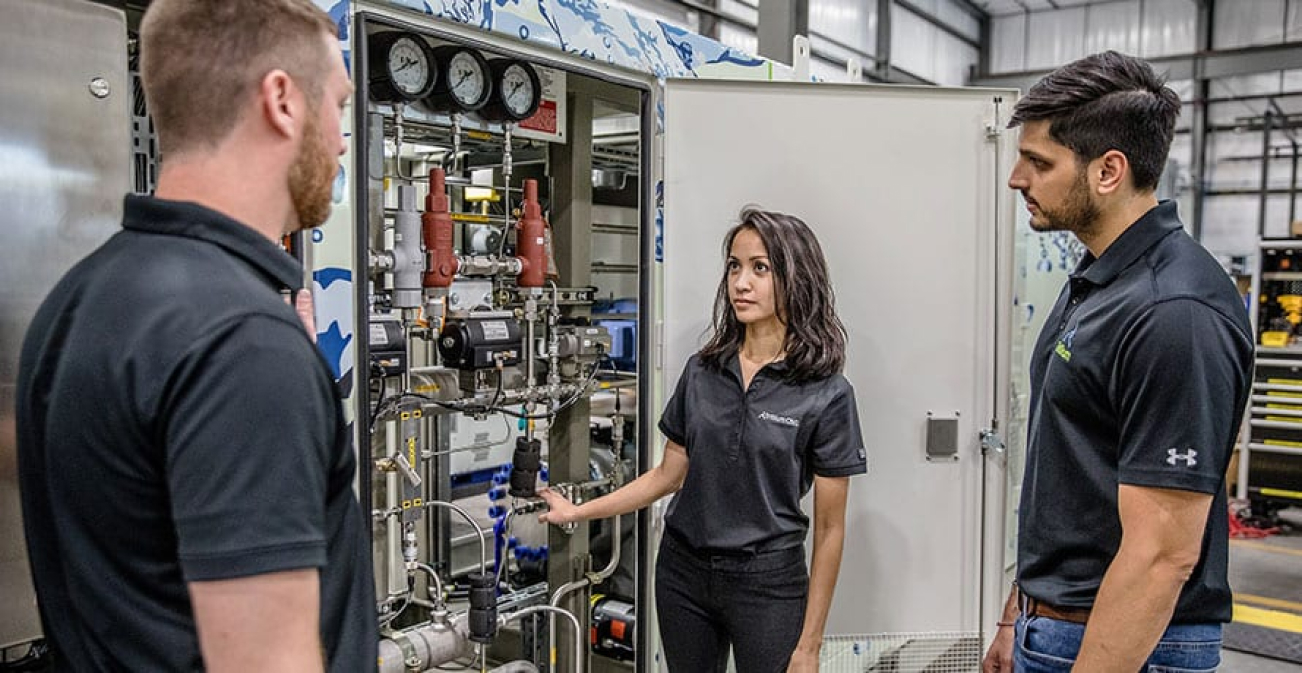
PDC offers complete compressor training for our customers. Training is available at your site or at PDC. Training consists of both classroom-style sessions as well as hands-on involvement. This provides the participants with theoretical and practical knowledge in the safe operation and maintenance of our compressor systems.
A typical PDC training course will cover but is not limited to the following course outline:
shooting